Table of Contents
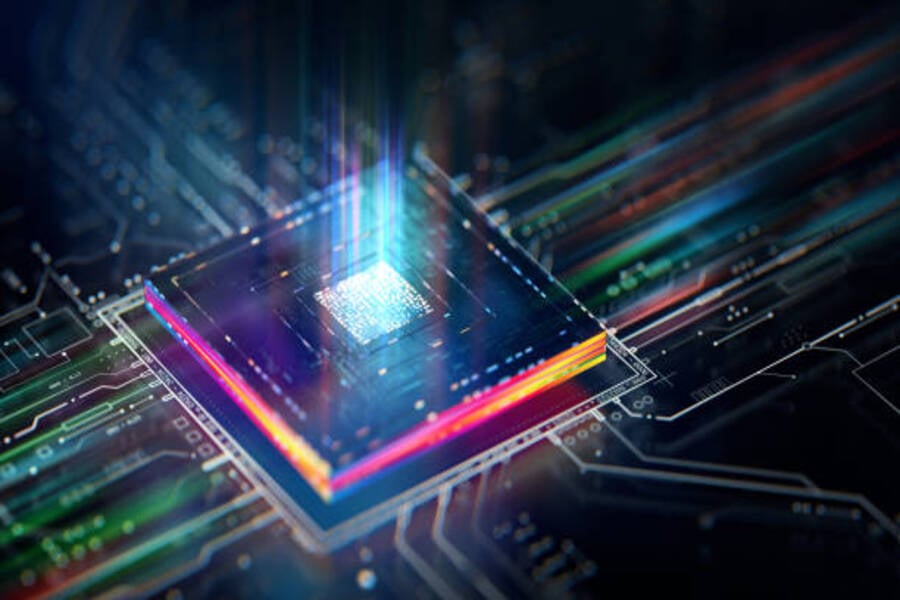
Understanding Molded Inductors: Indispensable Components in Modern Electronics
Molded inductors, commonly known as moulded inductors, are indispensable components in modern electronic circuitry. They are widely used in various electronic applications, including power supplies, switching regulators, and DC-to-DC converters, among others. In this article, we will discuss What is a molded inductor?, how it works, its advantages, and applications.
What is a Molded Inductor?
A molded inductor is a type of inductor that is enclosed or encapsulated in a molded plastic casing. It is also called a surface mount inductor or a chip inductor due to its compact size and surface mounting capability. The inductor is made up of a coil wound around a core, which generates a magnetic field when an electric current flows through it. The molded casing serves as a protection from physical and environmental damages, enhances thermal performance, and aids in mounting on a printed circuit board (PCB).
How does a Molded Inductor Work?
A molded inductor works on the principle of inductance- the property of an electrical conductor, which opposes the change in the current flowing through it. The coil wound around the magnetic core generates a magnetic field when current flows through it. This magnetic field stores energy in its system, and when the current stops flowing, the energy is released, resulting in a voltage boost. The inductor's inductance value depends on the number of coil turns, the core materials used, and the physical dimensions of the coil. In general, a larger number of coil turns results in higher inductance while a larger core made of magnetic materials such as iron, ferrite, or powdered iron increases the magnetic field's strength.
Advantages of Using Molded Inductors
Molded inductors offer various advantages over other types of inductors such as wire-wound or toroidal-types. The key advantages are:
- Compact size: Molded inductors are compact in size and can be surface-mounted on a PCB, saving valuable space for other components.
- High efficiency: Molded inductors have low resistance and produce negligible heat, making them highly efficient.
- Reliable: The molded casing protects the inductor from physical and environmental damages, making it more reliable and durable in harsh environments and high vibration applications.
- Cost-effective: Molded inductors are less expensive compared to other inductors, making them an attractive alternative for high volume production.
Applications of Molded Inductors
Molded inductors are used in various electronic circuits, including but not limited to:
- DC-DC converters
- Power supplies
- Radio communication systems
- Switching regulators
- Laptops, mobile phones, and other portable devices
Selection Considerations
When selecting a molded inductor, there are various factors to consider, including:
- Inductance value: The inductance value required depends on the specific application's needs and the circuit's electrical characteristics.
- Current rating: The maximum current rating of the inductor depends on the amount of current flowing through it.
- Frequency range: The inductor must be selected to operate within the desired frequency range of the application.
- Operating temperature range: The molded inductor must be rated to operate within the specific temperature range of the application.
Conclusion
In conclusion, molded inductors are indispensable components in modern electronics. They offer various advantages compared to other types of inductors, such as compact size, high efficiency, and low cost. Molded inductors are used in various applications, including power supplies, DC-to-DC converters, radio communication systems, and laptops. It is essential to consider various factors such as inductance value, current rating, frequency range, and operating temperature range when selecting a molded inductor for a specific application.