Table of Contents
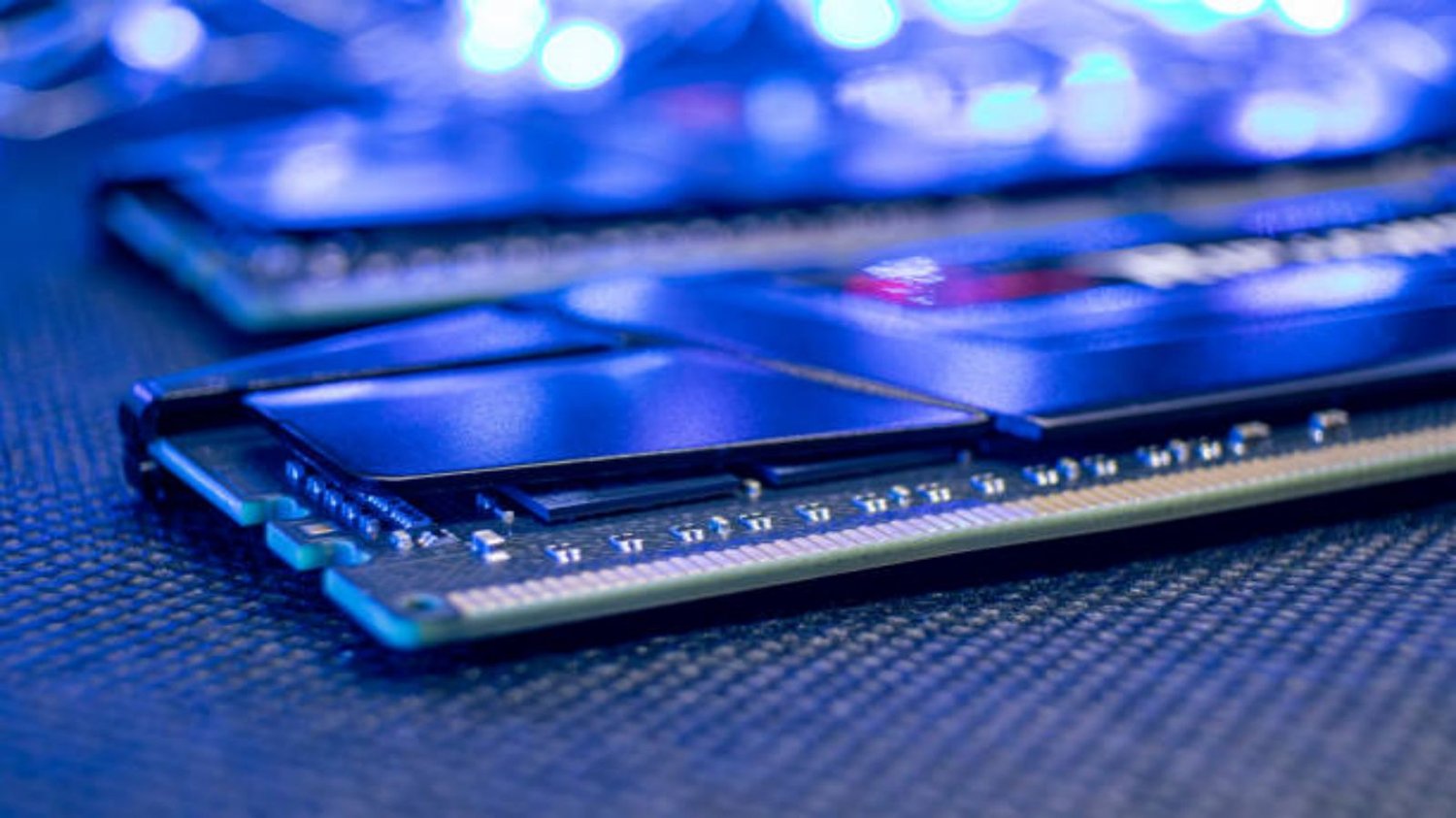
Understanding the molding power choke: An Introduction
In the world of electronics, the term "molding power choke" is frequently used, but what does it really mean? In this article, we will delve into the various aspects of molding power chokes, exploring their purpose, construction, and applications. Whether you are a seasoned engineer or a curious enthusiast, this comprehensive guide will equip you with the knowledge you need to understand and appreciate the power of molding power chokes.
The Functionality of a Molding Power Choke
A molding power choke is an indispensable component in electronic circuits, particularly in power supply designs. Its primary function is to store energy in the form of a magnetic field and release it when needed. This allows it to smooth out fluctuations in power supply currents, reduce electrical noise, and provide stable and reliable power to electronic devices.
Construction and Design Considerations
Molding power chokes are typically constructed using a combination of magnetic cores and windings. The magnetic core, often made of ferrite or powdered iron, provides the necessary magnetic properties. The windings, consisting of copper wires, are carefully wound around the core to optimize inductance and minimize resistance. The number of turns, wire gauge, and core material are key design considerations that affect the performance of the power choke.
The Importance of Inductance in Molding Power Chokes
Inductance is a crucial parameter in molding power chokes as it determines the ability of the choke to store energy. The higher the inductance value, the greater the energy storage capacity. This allows the power choke to effectively smooth out current fluctuations and minimize voltage ripples, ensuring a stable power supply. Inductance is typically measured in units called henries (H) or millihenries (mH).
The Impact of Saturation Current and DC Resistance
Saturation current and DC resistance are two vital characteristics to consider when selecting a molding power choke. Saturation current refers to the maximum current that a power choke can handle without significant loss of inductance. Exceeding the saturation current can lead to a drastic decrease in the choke's inductance, compromising its functionality. On the other hand, DC resistance determines the power dissipation and heat generation of the choke, with lower resistance values being more desirable.
Applications of Molding Power Chokes
Molding power chokes find applications in various electronic devices and systems. They are commonly used in power supplies for computers, telecommunication equipment, audio amplifiers, and industrial control systems. Additionally, they play a crucial role in filtering and reducing electromagnetic interference (EMI) generated by electronic circuits, ensuring optimal performance and compliance with industry standards.
The Advantages of Molding Power Chokes
Molding power chokes offer several advantages over other types of inductors. Firstly, their compact and robust design makes them suitable for use in space-constrained environments. The molding process provides mechanical protection to the internal components, enhancing durability and reliability. Moreover, their high energy storage capacity and low resistance make them efficient in reducing electrical noise and maintaining stable power supply voltages.
Selection and Installation Considerations
When selecting a molding power choke, it is crucial to consider factors such as the required inductance value, current rating, and physical size. It is also essential to ensure compatibility with the rest of the circuit and verify the choke's operating temperature range. During installation, proper soldering techniques should be followed to maintain electrical connections and prevent overheating or damage to the power choke.
The Future of Molding Power Chokes
As technology continues to advance, the demand for efficient and reliable power supplies grows. Molding power chokes are expected to play an increasingly important role in meeting these demands. Ongoing research and development aim to enhance the performance of molding power chokes, improving energy efficiency, reducing size, and further minimizing electrical noise.