Table of Contents
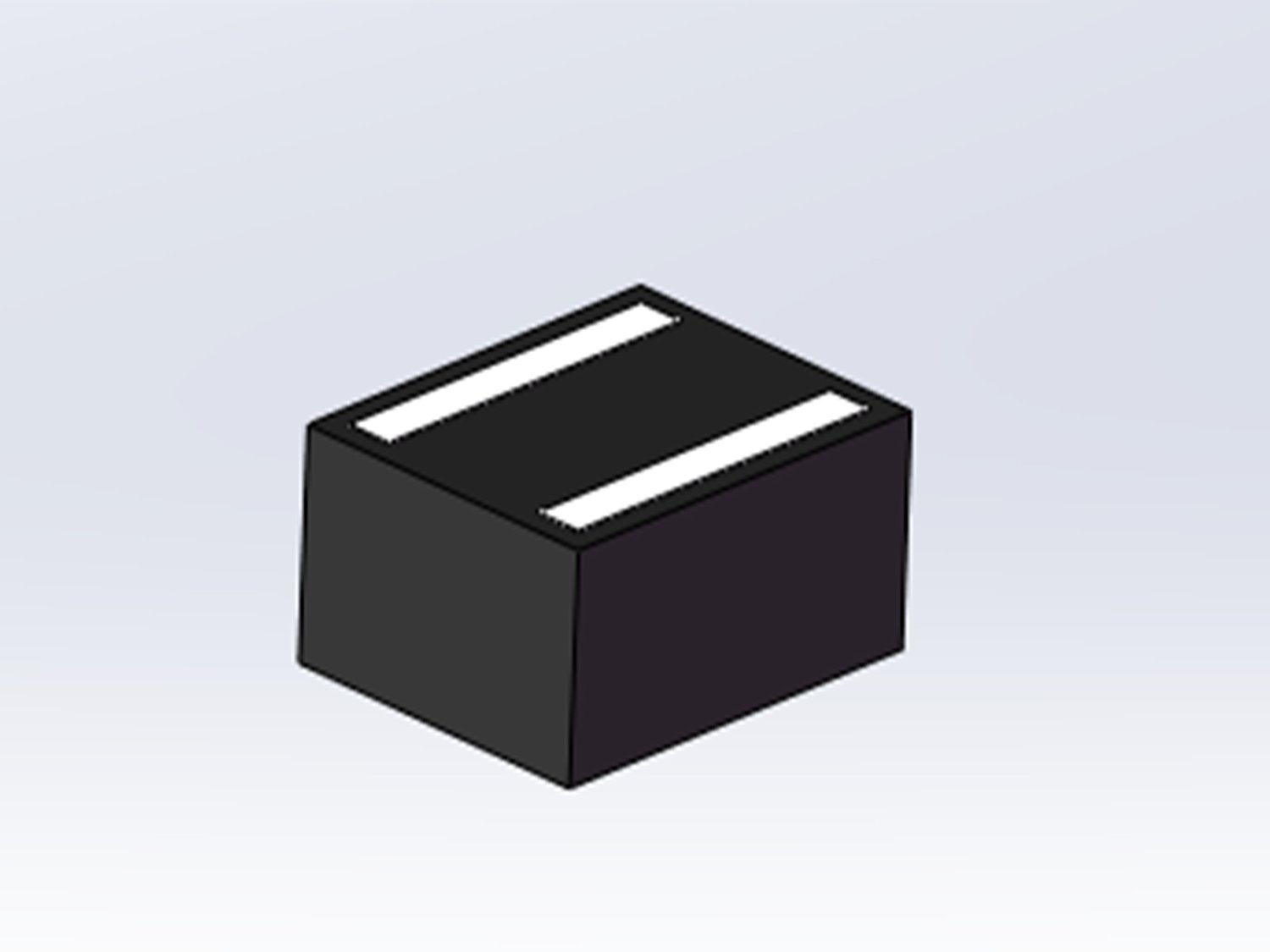
Understanding Molding Choke: A Crucial Component in Manufacturing
When it comes to manufacturing processes, various factors play a significant role in ensuring the production of high-quality and durable products. One such crucial element is molding choke, which contributes to the overall success of molding operations. In this article, we will explore the importance of molding choke and its impact on the manufacturing industry.
What is Molding Choke?
Molding choke refers to the process of controlling the flow of molten material during the molding process. It involves restricting the material flow to the desired areas of the mold cavity, ensuring precise and accurate product formation. By strategically placing chokes within the mold design, manufacturers can prevent defects such as flash, warpage, and inconsistent part dimensions.
Enhancing Product Quality and Consistency
By implementing molding choke techniques, manufacturers can significantly improve the quality and consistency of their products. The controlled flow of material ensures that the mold cavities are adequately filled, minimizing the chances of defects and inconsistencies. This results in products that meet the required specifications and customer expectations.
Preventing Flash and Parting Line Issues
Flash refers to the excess material that escapes the mold cavity and solidifies along the parting line. It is one of the most common defects in molding processes and can compromise the functionality and aesthetics of the final product. Molding choke plays a crucial role in preventing flash formation by precisely controlling the material flow and ensuring it remains within the designated areas.
Minimizing Warpage and Sink Marks
Warpage is a common issue in molded products, characterized by deformation or distortion of the part. It can occur due to uneven shrinkage or cooling of the material during the molding process. Molding choke helps in minimizing warpage by controlling the material flow and ensuring uniform distribution within the mold cavity. This results in products with minimal distortion and improved dimensional stability.
Controlling Part Dimensions and Tolerances
Precision is crucial in manufacturing various components, especially those that require tight tolerances. Molding choke allows manufacturers to have better control over the dimensions and tolerances of the final product. By strategically placing chokes in critical areas, they can ensure consistent and accurate part formation, meeting the specified requirements.
Optimizing Material Usage and Cost Efficiency
Molding choke also offers significant benefits in terms of material usage and cost efficiency. By controlling the material flow, manufacturers can minimize material waste and reduce overall production costs. This is particularly important when working with expensive or limited resources, as it helps maximize the utilization of materials and reduces the need for rework or scrap.
Reducing Cycle Time and Increasing Productivity
Efficiency is a key factor in manufacturing processes, and molding choke plays a vital role in improving productivity. By ensuring controlled and consistent material flow, manufacturers can reduce cycle time, allowing for faster production rates. This results in increased productivity and shorter lead times, enabling businesses to meet customer demands more effectively.
Considerations for Effective Molding Choke Design
Designing an effective molding choke system requires careful consideration of various factors. The location, size, and number of chokes must be determined based on the specific requirements of the product and the molding process. Additionally, the material properties, mold design, and process parameters should be taken into account to optimize the choke design for each unique application.
Continuous Improvement and Innovation
The field of molding choke is constantly evolving, with manufacturers and researchers continuously seeking innovative solutions to enhance molding processes. By staying updated with the latest advancements and adopting new technologies, businesses can further improve product quality, reduce defects, and optimize their manufacturing operations.
Conclusion
Molding choke plays a crucial role in ensuring the success of molding operations in the manufacturing industry. By controlling material flow, it enhances product quality, prevents defects, and improves overall productivity. Manufacturers must carefully consider the design and implementation of molding choke systems to optimize their manufacturing processes and stay competitive in today's market.