Table of Contents
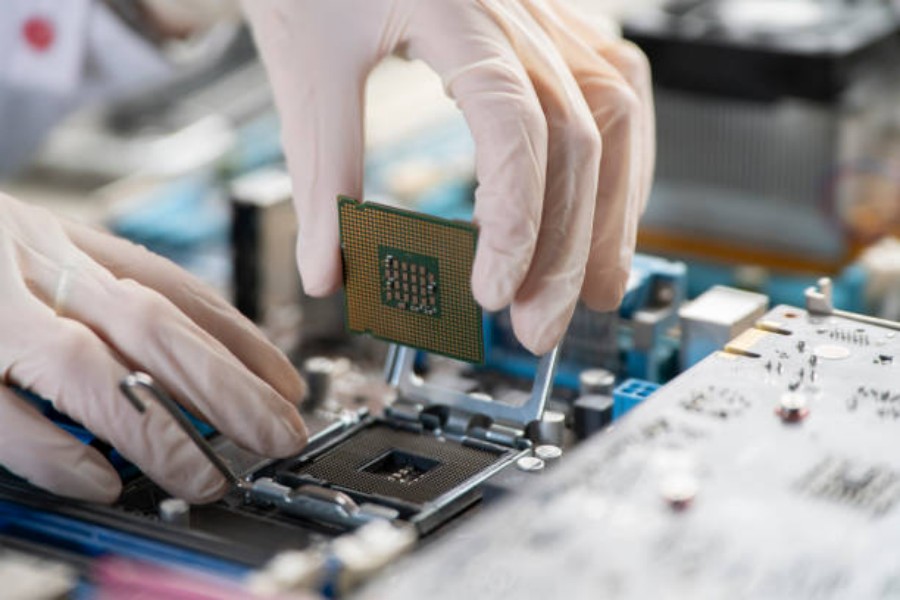
Introduction
A molding power choke, also known as a molded power inductor, is a type of passive electronic component that is used to suppress or filter high-frequency signals in electrical circuits. These chokes are made up of a coil of wire that is wrapped around a core material, which is usually made of ferrite.
Uses of Molding Power Choke
Molding power chokes are commonly used in various electronic devices, such as TVs, computers, and smartphones. They are used to filter out high-frequency noise and ensure stable and reliable power supply to the circuits. Some of the specific uses of these chokes include:
- EMC filters in power supplies and DC/DC converters
- Signal filtering in audio circuits and RF applications
- Noise suppression in motor control circuits and inverter systems
- Energy storage in power factor correction circuits
- Suppression of electromagnetic interference in automotive electronics
Benefits of Molding Power Choke
Using a molding power choke in your circuits can offer several benefits, such as:
- Reduced noise and interference that can cause malfunctions or reduce the lifespan of the electronic device
- Improved energy efficiency and reduced power loss due to lower heat dissipation
- Better voltage regulation and stability, which results in improved performance and longer lifespan of the device
- Higher reliability and longer lifespan of the device due to fewer breakdowns and malfunctions
Molding Power Choke vs. Traditional Choke
One of the main differences between a molding power choke and a traditional choke is the way they are constructed. A traditional choke is made up of a coil of wire that is wrapped around a magnetic core material, which is usually made of iron. On the other hand, a molding power choke uses a core material made of ferrite and is encapsulated in a plastic molding.
Another major difference is how they function. A traditional choke is primarily used to regulate the current flow in a circuit, while a molding power choke is used to filter out high-frequency noise. Additionally, molding power chokes have a much higher inductance value than traditional chokes, which makes them more effective in suppressing high-frequency noise.
Types of Molding Power Choke
There are different types of molding power chokes, each designed for specific applications. Some of the most commonly used types include:
- Surface mount power choke - used in PCBs and other small electronic devices
- Axial leaded power choke - used in audio circuits, power amplifiers, and inverters
- Toroidal power choke - used in power supplies, telecommunications equipment, and industrial automation systems
- Rod core power choke - used in automotive electronics and other high-temperature applications
Molding Power Choke Selection
Choosing the right molding power choke for your application requires careful consideration of various factors, such as:
- The inductance value required for the circuit
- The current rating based on the application
- The size and physical dimensions of the choke
- The temperature range and operating conditions of the application
Molding Power Choke Manufacturing
Molding power chokes are manufactured using a specialized process that involves winding the wire around the core material and encapsulating it in a plastic molding. The molding material can be made of different types of plastic, depending on the application requirements. Some of the commonly used molding materials include polypropylene, epoxy, and polyester.
Molding Power Choke Maintenance
Molding power chokes do not require any specific maintenance, as they are designed to function for long periods without any intervention. However, it is important to ensure that the chokes are properly installed in the circuit and that they are not subjected to any extreme temperatures or physical shocks that can damage the winding or the core.
Conclusion
Molding power chokes are an essential component in many electronic devices and circuits, as they provide electrical noise suppression and energy storage. Choosing the right type of choke for your application requires careful consideration of various factors, such as inductance value, current rating, and physical dimensions. By uclassing moldsing power choke, you can ensure improved performance, reliability, and energy efficiency for your electronic device.