Table of Contents
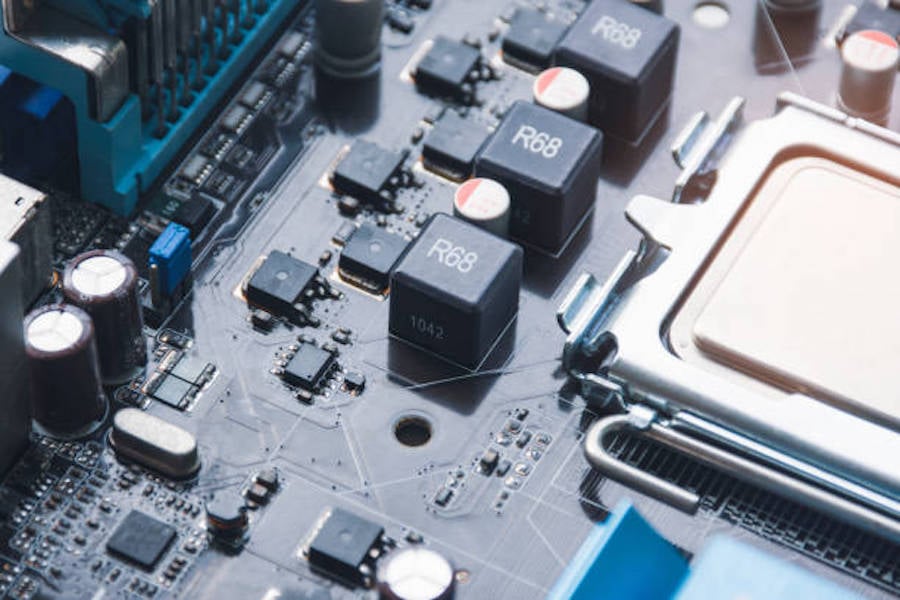
How to Troubleshoot Common Issues When Assembling Inductors
Introduction:
Inductors are essential components in electronic circuits, used for various purposes such as filtering, energy storage, and signal processing. However, when assembling inductors, it is common to encounter issues that can affect their performance. This article will guide you through troubleshooting these common issues, providing solutions to ensure the proper functioning of your inductors.
1. Understanding the Inductor Basics
Before diving into troubleshooting, it is crucial to have a solid understanding of the basics of inductors. An inductor is a passive electronic component that stores energy in the form of a magnetic field when current flows through it. It consists of a coil wound around a core material, typically made of iron or ferrite. Understanding the principles of inductance, magnetic fields, and core materials will help you diagnose and resolve issues more effectively.
2. Checking for Physical Damage
Physical damage can greatly affect the performance of an inductor. Inspect the inductor for any visible signs of damage, such as broken wires, loose connections, or bent cores. If you notice any damage, it is crucial to replace or repair the affected parts. Even minor physical damage can lead to significant issues, including increased resistance and reduced inductance.
3. Verifying Proper Coil Winding
The coil winding is a critical aspect of the inductor assembly process. Ensure that the wire is tightly wound around the core without any overlaps or gaps. Overlaps can cause short circuits, while gaps can result in increased resistance and reduced inductance. Use appropriate tools and techniques to achieve a uniform and tightly wound coil.
4. Evaluating Core Material Compatibility
The choice of core material plays a vital role in the performance of an inductor. Different core materials have varying magnetic properties and saturation levels. Ensure that the selected core material is compatible with the desired inductance value and operating frequency. Using an incompatible core material can lead to issues such as core saturation, increased losses, and decreased inductance.
5. Checking for Soldering Issues
Improper soldering can introduce various problems in the assembly of inductors. Check for soldering issues such as cold solder joints, insufficient solder, or solder bridges. These issues can cause poor electrical connections, increased resistance, and even shorts. Use proper soldering techniques, including the appropriate soldering iron temperature and flux, to ensure reliable connections.
6. Verifying Component Placement and Orientation
Incorrect component placement or orientation can lead to significant issues in inductor assembly. Ensure that all components, including the core, wires, and terminals, are properly placed and oriented according to the design specifications. Incorrect placement or orientation can result in reduced inductance, increased losses, and even short circuits.
7. Testing for Short Circuits
Short circuits can occur in inductors due to various reasons, such as overlapping windings, loose wires, or improper connections. To test for short circuits, use a multimeter in resistance mode. Measure the resistance between the terminals of the inductor. A low resistance reading indicates a short circuit and requires further investigation and repair.
8. Checking for Core Saturation
Core saturation is a condition where the magnetic core material reaches its maximum magnetic flux density, resulting in a significant drop in inductance. To check for core saturation, measure the inductance of the assembled inductor using an LCR meter. If the measured inductance is significantly lower than the expected value, it indicates core saturation. Consider using a larger core or a different core material to avoid saturation issues.
9. Testing Inductance and Impedance
Inductance and impedance are crucial parameters to evaluate the performance of an inductor. Use an LCR meter to measure the inductance and impedance of the assembled inductor. Compare the measured values with the expected values. Significant deviations indicate issues such as core saturation, winding errors, or soldering problems. Troubleshoot these issues accordingly to ensure optimal inductor performance.
10. Seeking Professional Assistance
If you have followed the troubleshooting steps mentioned above and are still experiencing issues with your assembled inductors, it might be time to seek professional assistance. Consulting an experienced electronics engineer or technician can help diagnose and resolve complex issues that might require specialized equipment or expertise. They can provide valuable insights and guidance to ensure the proper functioning of your inductors.
inductors, troubleshooting, assembling, physical damage, coil winding, core material, soldering, component placement, short circuits, core saturation, inductance, impedance How to Troubleshoot Common Issues When Assembling Inductors - Troubleshooting Guide Having trouble with your assembled inductors? This comprehensive article provides a step-by-step troubleshooting guide to help you identify and resolve common issues, ensuring optimal inductor performance.